Румянцев М.Ю., Захарова Н.Е., Сигачев С.И.
Аннотация. В статье рассмотрены проблемы выбора типа электропривода и опорных узлов для высокоскоростных электротурбомашин с частотой вращения ротора до 250000 об/мин. Показана целесообразность применения вентильных двигателей с возбуждением от постоянных магнитов на лепестковых газодинамических опорах. Рассмотрены особенности выбора материала постоянных магнитов для быстровращающихся роторов. Приведены данные о практических разработках высокоскоростных центробежных электрокомпрессоров, выполненных на кафедре ЭКАО МЭИ.
ВВЕДЕНИЕ В настоящее время при создании новых промышленных систем аэрации и водоподготовки, систем охлаждения, кондиционирования и вентиляции,автономных систем генерирования электроэнергии и т.д. отчётливо просматривается тенденция широкого использования в них электротурбомашин (ЭТМ) с частотой вращения ротора, исчисляемой десятками - сотнями тысяч оборотов в минуту. В ряде случаев повышенная частота вращения является обязательным требованием, невыполнение которого приводит к невозможности практического воплощения всего агрегата. Приступая к расчёту и проектированию сверхвысокоскоростных ЭТМ, разработчики сталкиваются с рядом специфических проблем, главными из которых являются: - Выбор типа электрической машины для привода ЭТМ.
- Выбор типа надёжных опорных узлов.
В настоящей статье рассмотрен опыт разработки ЭТМ на кафедре ЭКАО МЭИ. 1. ВЫСОКОСКОРОСТНЫЕ ЭЛЕКТРИЧЕСКИЕ МАШИНЫ В высокоскоростных ЭТМ с частотой вращения ротора до 250 тысяч об/мин возможно использовать только бесконтактные электрические машины (ЭМ), наиболее перспективными из которых на современном этапе развития науки и техники являются: - Асинхронный частотоуправляемый двигатель (АД) (AC Induction Motor);
- Вентильно-индукторный двигатель (ВИД) (Switched Reluctance Motor);
- Вентильный двигатель (ВД) с возбуждением от постоянных магнитов (Brushless DC Motor).
Как правило, при мощности более 300 Вт все указанные выше типы ЭМ выполняются трёхфазными. Другой их общей чертой является то, что переменное трёхфазное напряжение для электропитания обмоток ЭМ вырабатывается специальным электронным преобразователем, – инвертором, что предполагает выполнение всей системы электропривода по так называемой схеме со звеном постоянного тока с напряжением постоянного тока Ud. Как правило, электронный преобразователь осуществляет все необходимые функции по регулированию параметров движения ЭМ, реализации защит, коммутаций и т.д. Силовая часть инверторов выполняется практически по одинаковым схемам для всех названных типов двигателей. Отличия схем преобразователей проявляется в структуре и схемотехнике подсистемы управления, в количестве и назначении требуемых датчиков, в способах организации обратных связей. Коротко остановимся на отличительных особенностях бесконтактных ЭМ. Для частотоуправляемых АД характерно потребление намагничивающего (реактивного) тока, величина которого может составлять до 20% тока якоря в номинальном режиме. Это вызывает уменьшение коэффициента полезного действия (КПД) и коэффициента мощности (cosj). Другой особенностью АД является наличие потерь в цепи короткозамкнутой (беличьей) клетки ротора. Величина этих потерь достигает 8-10% от общих потерь в ЭМ и вызывает заметный нагрев ротора, что негативно сказывается на работе опорных узлов высокоскоростных ЭТМ, - подшипников качения и, особенно, подшипников с газовой смазкой (см. ниже). Несколько улучшить энергетическую эффективность АД можно, используя современные методы регулирования, в частности векторное управление. Но для реализации этих методов требуется усложнение системы управления, что зачастую экономически нецелесообразно. Кроме того известно, что габаритные размеры и конструкция всех элементов электрической машины, а также её весовые, экономические и эксплуатационные характеристики определяются так называемыми главными размерами- диаметром Dр [мм] и длиной lр [мм] активной части ротора [1]. Применительно к любому типу электродвигателя главные размеры можно получить из известного соотношения: 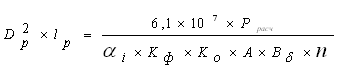
где Ррасч - расчётная мощность ЭМ,[Вт]; ai -расчётный коэффициент полюсного перекрытия; КФ - коэффициент формы кривой поля; Ко - обмоточный коэффициент; А - линейная нагрузка, [А/см]; Вd - индукция в воздушном зазоре [Тл]; n - частота вращения ротора [об/мин]. Обычно для АД индукция Вd составляет 0,5-0,6 Тл, что заметно ниже, чем в других типах ЭМ. Из-за этого удельный расход электротехнической стали и меди в АД больше, чем минимально возможный, да и потери них также значительны. В целом это приводит к увеличению габаритов и массы роторов, что применительно к высокоскоростным электроприводам компрессоров, негативно сказывается на работе газодинамических лепестковых подшипников. Несомненным достоинством частотоуправляемых АД является возможность использования для их изготовления готовых производств по выпуску АД, рассчитанных на питание от сети переменного тока 50 Гц и являющихся в настоящее время наиболее массовым видом ЭМ. В последнее время во многих отраслях промышленности получают распространение вентильные двигатели на базе индукторных машин. Принято считать, что главным достоинством индукторных двигателей является простота конструкции: зубцовые безобмоточный ротор и статор изготавливается из листов электротехнической стали. Пазы статора полностью открытые, что позволяет выполнять фазные обмотки сосредоточенными по конструктивной схеме "зубец-катушка”. Изготовление таких обмоток сводится к намотке на каркасах катушек, которые потом просто надеваются на зубцы статора. Крутящий момент в ВИД возникает за счёт разности магнитной проницаемости по продольной (Xd) и поперечной (Xq) осям ЭМ. Индукция в воздушном зазоре Вd для большинства ВИД определяется лишь параметрами электротехнической стали и может достигать 0,8-1,0 Тл, что приводит к экономии электротехнических материалов в 1,5 -2,0 раза по сравнению с АД. Различают ВИД с вентильным возбуждением (без специальной системы возбуждения) и ВИД с системой возбуждения. В первом случае поток возбуждения создаётся за счёт протекания тока намагничивания подобно тому, как это имеет место в АД. Несмотря на простоту конструкции подобные ВИД находят применение лишь в маломощных системах (до 300 Вт), в следствии низких энергетических характеристик. ВИД с системой возбуждения относятся к так называемым машинам с аксиальным потоком, в которых поток возбуждения, создаваемый либо катушкой возбуждения, либо постоянным магнитом, имеет осевую направленность. При этом неизбежно наличие нескольких паразитных воздушных зазоров, а кроме того величина главного осевого воздушного зазора d по чисто технологическим причинам всегда превышает величину d для ЭМ с радиальным потоком. За счёт этого возникают дополнительные потери на возбуждение, возрастает расход активных материалов. Другой отличительной особенностью ВИД является существенное влияние на протекание процессов электромагнитного преобразования энергии эффекта реакции якоря, что особенно негативно сказывается при регулировании работы электропривода. Как правило, все ЭТМ нуждаются в регулировании частоты вращения с диапазоном не менее 1:3÷1:5, поэтому для получения высоких значений КПД ВИД необходимо осуществлять регулирование угла коммутации силовых транзисторов инвертора. На практике это означает переход на принципы векторного управления, что существенно усложняет систему управления. Кроме того, массовому внедрению ВИД препятствует практически полное отсутствие отлаженных технологий, невозможность использования существующих технических решений и необходимость создания новых производств. С учётом того, что требуемая частота вращения ЭТМ мощностью до 10 кВт достигает 40000-250000об/мин, для уменьшения мощности потерь в стали статора желательно использовать ЭМ с минимальным числом полюсов. В тоже время, ВИД невозможно выполнить с двумя полюсами, поэтому мощность потерь в стали этих ЭМ будет всегда больше минимально возможной величины. Кроме того, в ВИД, как и в АД, имеются потери в роторе. Из названных выше бесконтактных ЭМ вентильные двигатели с возбуждением от постоянных магнитов (ПМ) теоретически обладают наибольшей энергетической эффективностью, т.к. не требуют дополнительной энергии на возбуждение (для этого используется энергия постоянных магнитов), не потребляют реактивного тока (cosj®1) [2]. Исследования показывают, что при прочих равных условиях, ВД по потребляемому из сети тока эффективнее примерно на 20%, чем АД и на 5-10%, чем ВИД. До недавнего времени основным фактором, препятствующим широкому внедрению ВД, являлась повышенная стоимость изготовления ротора с постоянными магнитами по сравнению с производством роторов для других типов ЭМ. Однако заметный прогресс, как в производстве самих магнитов, так и в технологии сборки роторов привёл в последнее время к заметному снижению стоимости ВД. Более того, многообразие современных магнитных материалов и магнитных систем позволяет предельно гибко и эффективно проектировать ВД под заданные приоритеты и критерии качества. Например, при использовании ферритовых магнитов можно получить предельно дешевую ЭМ. При использовании магнитов с высокой удельной энергией можно получить предельно высокие значения КПД и минимальный расход электротехнических материалов и т.д. Немаловажную роль играет и тот факт, что при организации производства ВД можно использовать уже имеющиеся и действующие производственные процессы и линии для производства АД. Например, можно применять оборудование, технологии, оснастку и другие составляющие технологического процесса для производства статоров ВД. При этом, благодаря свойствам современных ПМ и особенностям конструкций ВД, расход электротехнической стали и меди заметно снижается. При изготовлении электронного преобразователя для ВД также имеется возможность использовать уже имеющиеся схемотехнические решения силовой части И от серийных блоков для частотоуправляемых АД. Управляющая же часть преобразователя и система датчиков для ВД заметно проще, чем для АД. Таким образом, учитывая вышеизложенное, можно сделать выводы: 1. Для привода высокооборотных ЭТМ возможно использовать только бесконтактные электродвигатели. 2. Среди бесконтактных ЭМ вентильные двигатели с возбуждением от постоянных магнитов обладают наибольшей энергетической эффективностью, не имеют потерь в роторе,имеют наименьшую массу ротора и поэтому наиболее приемлемы для использования в электроприводе высокоскоростных ЭТМ. 2. Конструкции ротора высокоскоростных ВД В ВД высокоскоростных ЭТМ применяется классическая синхронная ЭМ, индуктором которой является расположенный на роторе постоянный магнит, а якорные обмотки располагаются на статоре [2]. При разработке высокоскоростных ВД необходимо учитывать, что ротора ЭТМ работают в условиях предельных механических (линейная скорость на поверхности ротора V ≥ 120 м/с) и температурных (T ≥150 o C) нагрузок. Поэтому, несмотря на многообразие современных магнитных материалов [3], высокоскоростные ротора можно выполнять только на основе двух типов ПМ: 1. Магниты на основе сплавов группы «Хром-кобальт-железо» типа 25Х15К, 27Х12К, 30Х23К и т.д. 2. Магниты на основе редкоземельных материалов группы «Самарий-кобальт» типа КС25, КС37, КС37А и т.д. В первом случае, благодаря уникальным для постоянных магнитов механическим свойствам материалов (предел прочности сплава 25Х15К – 400МПа, сплава 30Х23К – 750МПа, а монокристаллического хром-кобальтового сплава – 1500МПа), ротор может быть выполнен монолитным, т.е.целиком из постоянного магнита. Магнитные сплавы группы «Хром-кобальт-железо» допускают механическую обработку, включая нарезание резьбы и точение на обычных металлорежущих станках, что существенно упрощает технологию изготовления роторов и снижает стоимость машины в целом. Однако, магнитные сплавов невысоки (остаточная индукция Br = 0,8-1,2 Тл, коэрцитивная сила по намагниченности Hcм = 25-55 кА/м), ротора склонны к размагничиванию, что определяет специальные требования к конструкции ЭМ и структуре электронного преобразователя. Кроме того, технология производства указанных сплавов в настоящее время становится практически уникальной, их производство возможно лишь на небольшом числе предприятий России и их поставка может осуществляться лишь в ограниченном масштабе. Прекрасные магнитные свойства сплавов группы «самарий-кобальт» (остаточная индукция Br = 0,9-1,15 Тл, коэрцитивная сила по намагниченности Hcм = 1600-1700 кА/м), и высокая стабильность этих свойств в широком диапазоне температур делают самарий-кобальтовые магниты весьма перспективными для изготовления роторов высокоскоростных ЭТМ. В тоже время, прочностные свойства этих материалов невысоки, магниты весьма хрупкие (предел прочности 60-80 МПа), поэтому ротор на их основе может быть выполнен только составным с бандажом из немагнитного высокопрочного материала. Технология изготовления таких роторов более сложная и дорогая,однако получаемые ротора обладают прекрасными магнитными свойствами, малым весом и габаритами, что важно для проектирования высокоскоростных ВД.
3. Опоры высокоскоростных ЭТМ Одной из сложных проблем при создании высокоскоростных ЭТМ является обеспечение надежной работы их опор. Главные трудности здесь связаны с высокими скоростями вращения вала, с большими радиальными и осевыми нагрузками, с нагревом от рабочего тела и от тепловыделяющих элементов ЭМ. Во многих случаях опоры работают в исключительно тяжелых внешних условиях: переменных нагрузках, в широком диапазоне температур, воздействии вибрационных и ударных нагрузок. Традиционным типом опор являются подшипники качения с масляным охлаждением. Как правило, опоры являются наименее надежным звеном ЭТМ и определяют ее ресурс, который, как правило, в несколько раз меньше ресурса других узлов. Быстроходность подшипников качения, от которой зависят производительность и КПД турбомашины, ограничивается усталостными разрушениями, износом и нагревом рабочих элементов подшипников, имеющих место при трении качения. Кроме того, масляное охлаждение подшипников загрязняет рабочий газ и воздушную систему ЭТМ парами смазки, ухудшая работу теплообменных аппаратов. Накопленный в различных отраслях техники опыт использования бесконтактных высокоскоростных опор показывает, что из трех известных типов, – газодинамических, газостатических и электромагнитных, преимущественное применение нашли лепестковые газодинамические подшипники, являющиеся разновидностью газодинамических опор. Несущий газовый слой в таких подшипниках образован деформируемыми рабочими поверхностями – лепестками. Этот тип подшипников не нуждается ни во внешнем источнике сжатого газа, необходимом для работы газостатических подшипников, ни в источнике электроэнергии, питающем электромагнитные подшипники. Применение лепестковых газодинамических подшипников в турбомашинах позволяет решить ряд актуальных проблем: - обеспечить надежную работу подшипников в условиях высоких частот вращения,
- использовать турбомашины в условиях, недоступных для агрегатов с подшипниками качения, например, при наличии значительных внешних теплопритоков,
- исключить загрязнение сжимаемого газа парами масел,
- уменьшить массу машин за счет более компактной конструкции опорного узла и ликвидации системы смазки,
- увеличить ресурс турбомашин и упростить обслуживание машин.
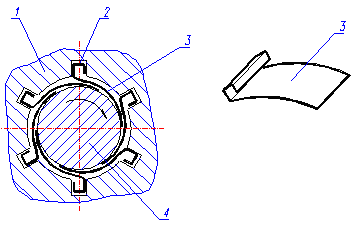 Рис.1. Конструкция радиального лепесткового газодинамического подшипника. На рис. 1 показана конструкция радиального лепесткового газодинамического подшипника. Лепесток арочного типа с коробчатой заделкой. В корпусе подшипника 1 выполнены продольные пазы 2, в которых с помощью хвостовиков закрепляются лепестки 3, изготовленные из пружинной стали. Лепестки, частично перекрывая друг друга, образуют ряд клиновых поверхностей. Предварительный натяг лепестков по валу связан с тем, что их радиус кривизны превышает радиус вала. При неподвижном вале 4, деформированные при сборке лепестки, стремясь распрямиться, прижимаются к валу средней частью и удерживают его в центре подшипника. На поверхности лепестков, обращенные к валу 4 с целью снижения при запуске ЭТМ трения наносится антифрикционное покрытие. В основе работы лепесткового газодинамического подшипника лежит эффект повышения давления в многоклиновом зазоре, возникающем при относительном перемещении поверхностей. Вращающийся ротор увлекает воздух в конфузорные зоны между валом и лепестками, при увеличении частоты вращения давление воздуха в этих зонах возрастает и, наконец, становится достаточным для отжатия лепестков отвала. Всплытие ротора и образование несущего газового слоя между лепестками и валом происходит при частоте вращения, соответствующей возникновению гидродинамического клина. Дальнейшее увеличение частоты вращения приводит к росту толщины газового слоя, равнодействующая давлений превышает вес ротора, воспринимаемый подшипником, и усилие предварительного натяга лепестков по валу. Скорость всплытия в зависимости от геометрии лепесткового газодинамического подшипника и составляет 3÷10 м/с. Несущая способность лепесткового газодинамического подшипника зависит от профиля газового слоя, формирующегося в соответствии с толщиной, длиной и степенью перекрытия лепестков, рабочими зазорами и режимом работы. Особенностью лепесткового газодинамического подшипника является способность к изменению профиля рабочего зазора в соответствии с режимом работы. Податливость и малая масса лепестков позволяют им легко отслеживать колебания ротора, вызываемые дисбалансом или внешними возмущениями, и надежно работать в условиях тепловых деформаций корпусов и при попадании в рабочие зазоры грязи. При сближении ротора с лепестком давление в газовом слое увеличивается, поэтому лепесток деформируется. Когда ротор удаляется от лепестка, давление в газовом слое падает и лепесток приближается к ротору. При этом снижение тангенциальной составляющей реакции газового слоя за счет самоустановки лепестков позволяет успешно подавлять автоколебания и значительно повышать частоты вращения ротора. Демпфирование колебаний в лепестковом газодинамическом подшипнике происходит при трении лепестков между собой и корпусом. Дополнительное демпфирующее действие оказывают газовые слои, расположенные между лепестками и корпусом подшипника, а также силы, возникающие при деформации лепестков. Привозникновении колебаний вала лепестки «отслеживают» эти колебания, т.е. вал вместе с несущим газовым слоем прецессирует в упругом пакете лепестков. Многочисленные зоны сухого трения, образующиеся при относительном смещении лепестков в процессе их деформирования, рассеивают колебательную энергию вала, обеспечивая его устойчивое вращение. Отсутствие механических контактов между валом и лепестками позволяет реализовывать очень высокие рабочие частоты вращения вала при обеспечении большого ресурса. Износ антифрикционного покрытия опор имеет место только в моменты всплытия и останова ротора. Анализ состояния опор, проведенный после окончания ресурсных испытаний в объеме 30000 циклов «пуск – останов», показал, что износ покрытия составляет 30% толщины слоя, причем 20%-ый износ пришелся на приработку в период первых 50 циклов. В настоящее время на кафедре ЭКАО МЭИ практически решены задачи проектирования и расчета лепестковых газодинамических подшипников, а также технологические проблемы изготовления и подбора необходимых материалов ипокрытий. Создан ряд подобных опор для роторов массой 0,3÷17,0 кг. Турбомашины с лепестковыми опорами успешно прошли испытания на работоспособность в наземныхи высотных условиях в составе оборудования летательных аппаратов, а также испытания на виброустойчивость и вибропрочность в диапазоне частот 5÷2000 Гц, ударную прочность с ускорением до 12g, влагоустойчивость, термоциклирование от-60 до +80 0C.
4. Структура электропривода компрессора. Как было указано выше, электропривод ЭТМ целесообразно выполнять на основе так называемого вентильного двигателя, под которым в мировой практике подразумевается электромеханическая система, состоящая из: - синхронной электрической машины, ротор которой выполняется на основе постоянных магнитов;
- датчика положения ротора (ДПР), установленного на валу ЭМ;
- электронного преобразователя (ЭЛП), осуществляющего подключение фаз ЭМ к источнику электроэнергии и формирование необходимых процессов преобразования энергии.
Работа столь сложных электромеханических систем характеризуется протеканием в них процессов различной физической природы: механических, электрических, тепловых и других, постоянные времени и интенсивность протекания каждого из этих процессов отличаются на несколько порядков. Вместе с тем, каждый из них вносит свой определенный вклад в выходные характеристики системы в целом, такие как массо-габаритные, энергетические, надёжность и т.д. Поэтому при проектировании ЭТМ необходима чёткая увязка свойств отдельных элементов между собой и с требуемыми характеристиками системы в целом. Особенно важно точное определение параметров и свойств этих отдельных элементов именно на этапах НИР и ОКР, когда еще не до конца отработаны технические решения и характеристики системы могут существенно изменяться в зависимости от свойств элементов. Получить же данные об этих свойствах практически невозможно без изготовления и последующих экспериментальных исследований макетных (опытных) образцов. Функциональная схема ЭТМ приведена на рис.2., где обозначено: БП - входной блок питания, ЭЛП – электронный преобразователь с информационно-управляющей подсистемой ИУП и датчиком тока ДТ, ЭМ - электрическая машина с установленными на валу датчиком положения ротора ДПР и центробежным компрессорным колесом (колёсами) КК.
БП предназначен для преобразования напряжения сети переменного тока, в постоянное напряжение Ud, к шинам которого подключается ЭЛП. В состав БП входят блок коммутационно-защитной аппаратуры (в простейшем случае - трехфазный управляемый контактор), трехфазный диодный выпрямитель В, и низкочастотный фильтр Ф (в простейшем случае – C-типа). При переходе к системам постоянного тока (в том числе, бортовым) из структуры БП исключается лишь выпрямитель. ЭЛП обеспечивает электропитание фаз ЭМ переменным напряжением, т.е. основной функцией силовой части СЧ ЭЛП является инвертирование напряжения Ud постоянного тока. Частота этого напряжения определяется частотой вращения ЭМ, а количество фаз – структурой и фазностью ЭМ. Обязательной функцией ЭЛП является регулирование (в простейшем случае ограничение) тока, протекающего через силовые транзисторы и фазы ЭМ. Наиболее часто это регулирование осуществляется методом широтно-импульсной модуляции (ШИМ) времени открытого состояния силовых транзисторов ЭЛП. Для получения информации о величине коммутируемого силовыми транзисторами тока в ВД достаточно установить датчик тока ДТ- (см. рис.2) в шину постоянного тока. Обычно в качестве ДТ используют бесконтактные приборы, основанные на эффекте Холла. Учитывая тот факт, что фазные обмотки высокоскоростных ВД обладают чрезвычайно малыми значениями индуктивного и активного сопротивлений, частота ШИМ может достигать нескольких десятков кГц, что является предельной величиной даже для современных полупроводниковых приборов. Поэтому к проектированию СЧЭЛП необходимо подходить весьма тщательно. Для ВД с напряжением в шине постоянного тока свыше 300В силовая часть ЭЛП выполняется в большинстве случаев на биполярных транзисторах с изолированным затвором (IGBT). При Ud ≤ 300В предпочтительней использовать полевые транзисторы (MOSFET). К сожалению, в настоящее время отечественная промышленность не производит подобные полупроводниковые приборы, поэтому в ЭЛП необходимо применять комплектующие зарубежного производства, например, фирм SIEMENS (Германия), International Rectifier (США), HITACHI (Япония) и т.д. ИУП ЭЛП предназначена для выработки сигналов управления транзисторами СЧ с целью формирования требуемых параметров движения электропривода, обеспечения необходимых защит и индикации режимов работы ВД. Основными функциями ИУП ЭЛП являются: - Ограничение тока, защита от КЗ.
- Стабилизацияи регулирование частоты вращения ЭМ.
- Защита ЭМ от повышения частоты вращения.
- Защита от понижения частоты вращения ниже допустимой по условиям работы ЛГО.
- Индикация аварийных режимов.
- Возможность как ручного, так и внешнего управления от внешних устройств и датчиков.
- Визуализация параметров работы электропривода.
Элементной базой ИУП могут быть как программируемые микропроцессорные устройства, так и специализированные микросхемы управления ВД. Специалисты каф. ЭКАО МЭИ (руководитель Румянцев М.Ю.) имеют необходимый опыт разработки, как силовой, так и информационно- управляющей частей ЭЛП.
5. ПРАКТИЧЕСКИЕ РАЗРАБОТКИ ЭТМ в МЭИ Работы по созданию высокоскоростных ЭТМ на базе ВД на ЛГО проводятся в МЭИ с 1993 года и базируются на многолетнем опыте разработки вентильных электроприводов авиационного и специального назначения. Работы выполнялись под руководством к.т.н., доцента Морозова В.А., а с 2000 г., - к.т.н., с.н.с. Румянцева М.Ю. Активное участие в разработке высокоскоростных ЭТМ принимали сотрудники кафедры Нестеров М.В., Головин Д.Н., Апаров М.А. и др. С другой стороны, проектирование и производство лепестковых газодинамических подшипников также имеют длительную историю и выполнялось специалистами кафедры под руководством к.т.н. Захаровой Н.Е. Объединение на базе кафедры ЭЭЛА МЭИ этих специалистов позволило комплексно решать задачи разработки ЭТМ. Результатом работ в МЭИ явилось создание методик расчёта и проектирования высокоскоростных ВД на ЛГО и электронных устройств управления ими, разработка стендов для экспериментальных исследований ЭТМ и программ испытаний ЭТМ, разработка серии ЛГО для ЭТМ мощностью 0,3-120 кВт, а также разработка ряда опытных образцов высокоскоростных центробежных электрокомпрессоров. Одноступенчатый воздушный электрокомпрессор ЭКВС мощностью 3,5 кВт, с частотой вращения 120000 об/мин был разработан по заказу компрессоростроительной фирмы «НОЭМИ» для использования в качестве воздуходувки. На рис. 3 дан внешний вид этого компрессора, а в таблице 1 приведены его характеристики. 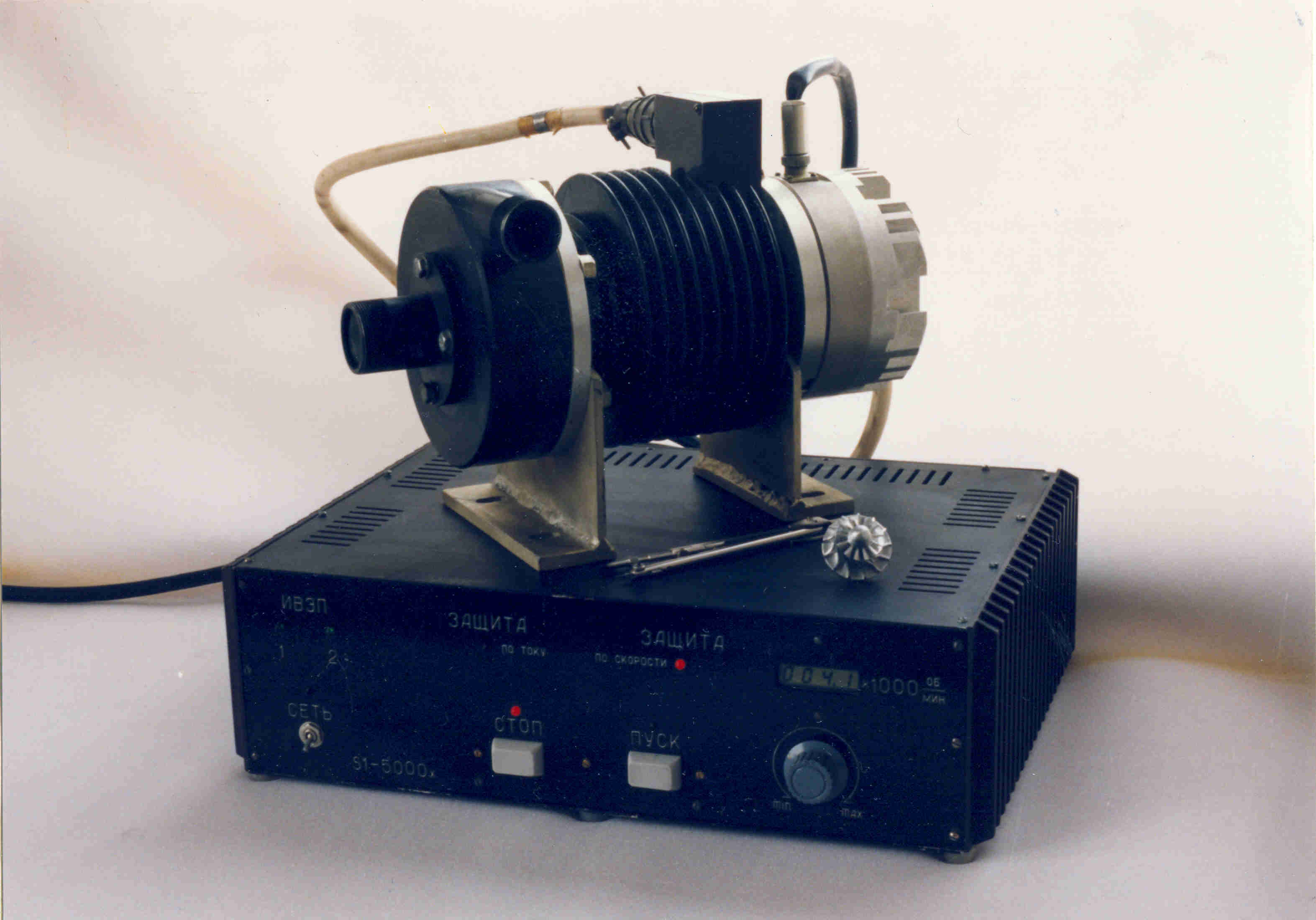
Рис.3. Одноступенчатый турбовентилятор мощностью 3,5 кВт. Частота вращения ротора 120000 об/мин.
Таблица 1. Технические характеристики ЭКВС-3,5
Мощность на валу | 3500 Вт
| Номинальная частота вращения | 120000 об/мин
| Диапазон регулирования частоты вращения | 40000...120000 об/мин
| Производительность | 2.5 м3/мин
| Степень повышения давления | 1,8
| Конструкция ротора | монолитный
| Материал магнита | 25Х15К
| Напряжение питания | 220В, 50 Гц
| Режим работы | Длительный
| Количество ступеней сжатия | 1
| Ресурс | 50000 час
| Габариты электрокомпрессора (без штуцеров) | ∅ 150 мм × 280 мм
| Габариты электронного блока | 500×420×150 мм
| Вес электрокомпрессора | 12 кг
|
По заказу Федерального ядерного центра (г. Саров) разработаны образцы воздушных электрокомпрессоров мощностью 300 Вт с частотой вращения 90000 об/мин для использования в системах генерирования электроэнергии на топливных элементах. В таблице 2 приведены характеристики компрессора, а на рис. 4 – его внешний вид.
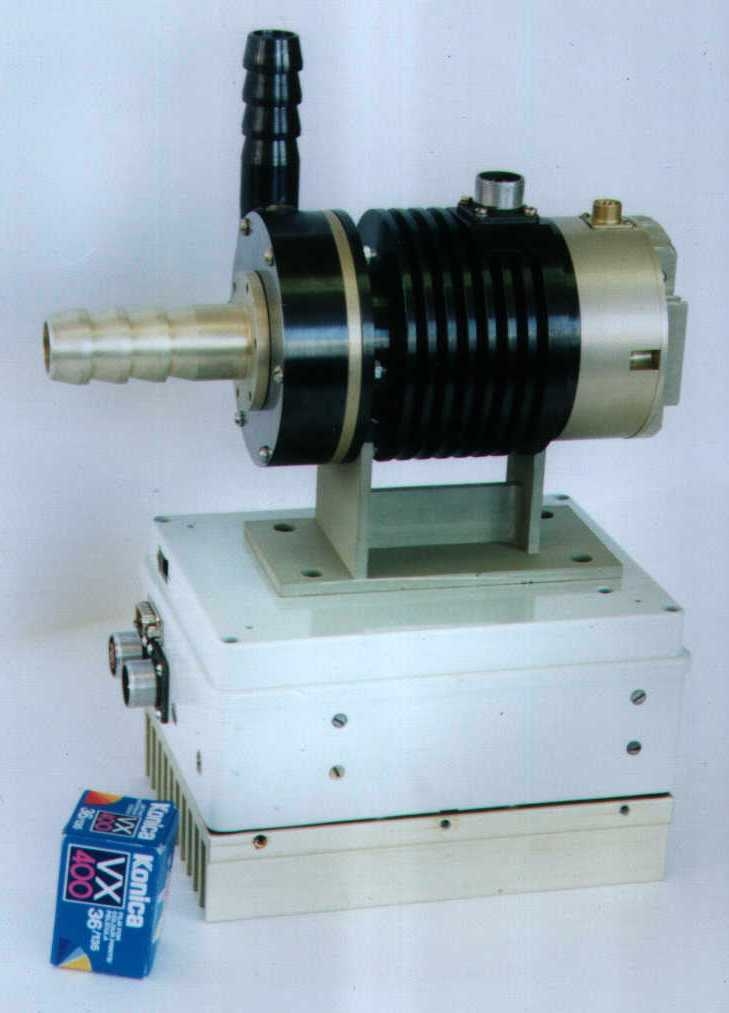
Рис.4. Воздушный электрокомпрессор мощностью 350 Вт. Частота вращения ротора 90000 об/мин.
Таблица 1. Технические характеристики ЭКВС-3,5
Мощность на валу | 350 Вт
| Номинальная частота вращения | 90000 об/мин
| Диапазон регулирования частоты вращения | 20000...95000 об/мин
| Производительность | 10...50 м3/час
| Степень повышения давления | 0,03...0,2
| Конструкция ротора | Сборный с бандажом
| Материал магнита | КС-25
| Напряжение питания | 27 В постоянного тока
| Режим работы | Длительный
| Количество ступеней сжатия | 1
| Ресурс | 50000 час
| Габариты электрокомпрессора (без штуцеров) | ∅ 100 мм × 160 мм
| Габариты электронного блока | 200×150×160 мм
| Вес электрокомпрессора | 5,2 кг
|
СПИСОК
ЛИТЕРАТУРЫ
1. Балагуров В.А. Проектирование…
2. А. Н. Ледовский. Электрические машины с высококоэрцитивными постоянными
магнитами. М., Энергоатомиздат,1985г.
3. Прецизионные
сплавы. Справочник // Под ред. Молотилова Б.В. – М.: Металлургия, 1983.
4. Захарова Н.Е.,
Румянцев М.Ю. и др. Безмасляные турбомашины на базе сверхвысокоскоростных
вентильных электроприводов// Вентильные электромеханические системы. Сб.
докладов 6-го научно-практического семинара. М.: Изд-во МЭИ, 1996.-С.35-39.
|